خوردگی (corrosion) یک مسئله حیاتی در صنایع نفت، گاز، پتروشیمی و انرژی است، زیرا میتواند به طور قابل توجهی بر عملکرد تجهیزات، ایمنی و راندمان عملیاتی کلی تاثیر بگذارد. مکانیسمهای خوردگی که در این بخشها اتفاق میافتد از نظر شدت و تاثیر متفاوت است و درک علل، طبقهبندیها و اقدامات پیشگیرانه را ضروری میسازد.
این مطلب به بررسی مفاهیم مهندسی خوردگی (corrosion) و روشهای مختلف حفاظت در برابر خوردگی میپردازد و توضیح میدهد که چگونه راهحلهای پیشرفتهای مانند ایمن بالابران کهکشان میتوانند به مدیریت موثر این چالشها کمک کنند.
خوردگی (corrosion) چیست؟
خوردگی به تخریب یا زوال تدریجی مواد، معمولا فلزات، در اثر واکنشهای شیمیایی با محیط آنها اطلاق میشود. در محیطهای صنعتی، این اغلب شامل واکنش فلزات با رطوبت، هوا یا مواد شیمیایی است که منجر به تشکیل زنگ یا سایر محصولات خوردگی میگردد.
این فرآیند الکتروشیمیایی است که معمولا شامل یک آند، کاتد و الکترولیت است و الکترونها از طریق یک مدار خارجی از آند به کاتد جریان مییابند. خوردگی اغلب توسط عوامل محیطی خشن مانند رطوبت زیاد، قرار گرفتن در معرض آب شور، یا وجود مواد شیمیایی اسیدی یا بازی تسریع میشود.
اثرات آن بر داراییهای صنعتی، به ویژه در بخش نفت و گاز، میتواند منجر به خرابی تجهیزات، خرابی و تعمیرات پرهزینه شود. بنابراین، درک مکانیسمهای خوردگی و انواع مختلف خوردگی برای حفظ یکپارچگی و طول عمر داراییها حیاتی است.
طبقه بندی خوردگی چیست؟
خوردگی را میتوان بر اساس مکانیسم، ظاهر یا مواد درگیر به روشهای مختلفی طبقه بندی کرد. رایجترین طبقه بندیها عبارتند از:
۱. خوردگی الکتروشیمیایی:
زمانی اتفاق میافتد که دو فلز مختلف با یک الکترولیت در تماس باشند که منجر به جریان الکترون و تخریب یک فلز میشود.
۲. خوردگی گالوانیک:
زیر مجموعهای از خوردگی الکتروشیمیایی، زمانی اتفاق میافتد که دو فلز مختلف با پتانسیلهای الکتروشیمیایی متفاوت در تماس باشند و باعث میشوند یکی سریعتر از دیگری خورده شود.
۳. خوردگی شیاری:
در فضاهای محدودی که الکترولیت راکد میشود، مانند اتصالات، پیچ و مهره یا جوش، رخ میدهد که منجر به خوردگی تسریع در آن مناطق میشود.
۴. خوردگی حفرهای:
شامل تشکیل حفرههای کوچک و موضعی بر روی سطح فلز است که در صورت عدم توجه میتواند منجر به آسیب ساختاری شدید شود.
۵. خوردگی یکنواخت:
خوردگی یکنواخت، رایج ترین شکل از خوردگی است به طور یکنواخت در سراسر سطح رخ میدهد، که اغلب منجر به نازک شدن تدریجی مواد میشود.
شکلهای دیگر خوردگی شامل ترک خوردگی تنشی (SCC)، خوردگی بین دانهای و شکنندگی هیدروژنی است که هر کدام علل و اثرات منحصر به فردی بر روی مواد دارند.
چهار نوع اصلی خوردگی (corrosion) چیست؟
درک چهار نوع اصلی خوردگی برای کاربردهای صنعتی بسیار مهم است. این انواع عبارتند از:
۱. خوردگی یکنواخت:
همانطور که از نام آن پیداست، خوردگی یکنواخت بر کل سطح به طور یکنواخت تاثیر میگذارد، معمولا به دلیل قرار گرفتن در معرض یک محیط خورنده. این قابل پیشبینی ترین شکل است و اغلب در لولهها، تانکرها و مخازن رخ میدهد.
۲. خوردگی حفرهای:
خوردگی حفرهای موضعی است و منجر به ایجاد حفرهها یا چالههای کوچک در مواد میشود. اغلب به دلیل وجود کلریدها یا محیطهای اسیدی ایجاد میگردد که منجر به تجزیه سطح فلز میشود.
۳. خوردگی شیاری:
این شکل در مناطقی رخ میدهد که الکترولیت در فضاهای کوچک مانند اتصالات، پیچ و مهره یا ترک به دام افتاده است. کمبود اکسیژن و غلظت عوامل خورنده باعث تسریع فرآیند خوردگی در این شکافها میشود.
۴. خوردگی گالوانیک:
هنگامی که دو فلز غیرمشابه در حضور الکترولیت در تماس باشند، ممکن است یک فلز سریعتر از دیگری خورده شود. فلز آندی بیشتر خورده میشود، در حالی که فلز کاتدی محافظت میگردد. این معمولا در تاسیساتی که فلزاتی مانند فولاد و آلومینیوم در تماس هستند دیده میشود.
۱۰ نوع خوردگی چیست؟
در حالی که درک چهار نوع اصلی خوردگی (corrosion) ضروری است، چندین نوع دیگر نیز وجود دارد که میتوانند چالشهای منحصر به فردی را در محیطهای صنعتی ایجاد کنند. این موارد عبارتند از:
۱. ترک خوردگی تنشی (SCC):
زمانی اتفاق میافتد که یک ماده در معرض تنش کششی که محیط خورنده قرار میگیرد و منجر به تشکیل ترکهایی میشود که میتوانند در طول زمان منتشر شوند.
۲. خوردگی بین دانهای:
این نوع در امتداد مرزهای دانه یک فلز رخ میدهد، اغلب به دلیل عملیات حرارتی نامناسب یا قرار گرفتن در معرض مواد شیمیایی خاص، که باعث ضعیف شدن مواد میگردد.
۳. شکنندگی هیدروژن:
وقتی اتمهای هیدروژن به فلز جذب میشوند، میتوانند باعث شکننده شدن مواد و ترک خوردن آن تحت تنش شوند، به ویژه در محیطهای پرفشار مانند خطوط لوله نفت و گاز.
۴. خوردگی فرسایشی:
این نوع ناشی از اثرات ترکیبی سایش و خوردگی مکانیکی است که اغلب در جریانهای پر سرعت مایعات یا گازها دیده میشود که میتوانند لایه اکسید محافظ روی مواد را فرسایش دهند.
۵. خوردگی میکروبی(MIC):
این شکل به دلیل وجود میکروارگانیسمهایی مانند باکتریها، قارچها یا جلبکها به وجود میآید که از طریق فرآیندهای متابولیکی خود، خوردگی را تسریع میکنند.
۶. خوردگی سایشی:
ناشی از حرکت نسبی بین دو ماده در تماس تحت بار، خوردگی فرسایشی منجر به آسیب سطح و افزایش سایش میشود.
۷. خوردگی گالوانیک:
همانطور که قبلا ذکر شد، این اتفاق زمانی رخ میدهد که دو فلز غیرمشابه با یک الکترولیت در تماس باشند که منجر به خوردگی فلز آندیتر میشود.
۸. شستشوی انتخابی (زنگ زدایی):
این در آلیاژهای برنج زمانی اتفاق میافتد که روی به طور انتخابی از آلیاژ شسته میشود و ساختار مس متخلخلی باقی میماند که میتواند تحت تنش از بین برود.
۹. خوردگی فرسودگی:
اغلب در تجهیزاتی که در معرض دماهای بالا قرار دارند دیده میشود، خوردگی فرسودگی زمانی رخ میدهد که لایه اکسید محافظ فلز به دلیل گرما آسیب ببیند و مواد را در معرض خوردگی سریع قرار دهد.
۱۰. خوردگی دو فلزی:
این اتفاق زمانی رخ میدهد که دو فلز مختلف به هم متصل شوند که باعث میگردد فلز واکنش پذیرتر با سرعت بیشتری خورده شود.
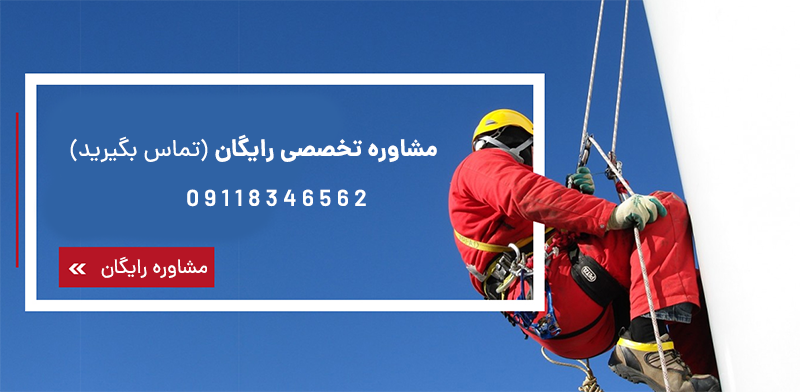
۸ شکل خوردگی چیست؟
اشکال خوردگی (corrosion) اغلب بر اساس ظاهر یا رفتارشان طبقه بندی می شوند و عبارتند از:
- خوردگی عمومی: یک شکل یکنواخت و گسترده از خوردگی که به طور یکنواخت در سراسر سطح یک ماده رخ میدهد.
- خوردگی حفرهای: خوردگی موضعی که منجر به تشکیل حفرههای کوچک روی سطح میگردد.
- خوردگی شکاف: در فضاهای محدود، مانند اتصالات پیچ و مهره ای یا ترک، که در آن الکترولیت راکد می شود، رخ میدهد.
- خوردگی گالوانیک: نوعی خوردگی است که زمانی اتفاق میافتد که دو فلز غیرمشابه با یک الکترولیت در تماس باشند.
- ترک خوردگی تنشی (SCC): ایجاد ترک تحت تنش در یک محیط خورنده.
- خوردگی بین دانهای: خوردگی در امتداد مرزهای دانه فلزات.
- تردی هیدروژنی: در اثر جذب هیدروژن ایجاد می شود و فلزات را شکننده و مستعد ترک خوردن میکند.
- خوردگی فرتینگ: در اثر حرکت نسبی بین دو ماده در تماس تحت بار ایجاد میشود.