بازرسی جوشکاری در بسیاری از صنایع و کاربردها ضروری است. انتظار میرود بازار جهانی تجهیزات جوش تا سال ۲۰۳۰ به حدود ۲۸ میلیارد دلار برسد و افزایش تقاضا برای فولاد جوش داده شده در سازههای مسکونی و تجاری احتمال رشد را در این دوره افزایش خواهد داد. جوشهای ایمن و قابل اعتماد برای حفظ کیفیت یک محصول یا نصب بسیار مهم هستند. تست استحکام جوش یکی از اجزای مهم هر جوشکاری کاربردی است که یکپارچگی ساختار و قابلیت اطمینان اتصال را بررسی کرده و با استانداردسازی ارزیابی جوشکاری در بسیاری از کاربردها، ایمنی و ثبات را ارتقا میدهد.
چرا بازرسی جوشکاری مهم است؟
نقص یا ضعف در جوش میتواند عواقب قابل توجهی از جمله آسیب و خرابی محصول داشته باشد. دانستن نحوه بازرسی جوش در قبل، حین و بعد از جوشکاری برای اطمینان از اینکه محصولات و تجهیزات قابل اعتماد باقی میمانند و میتوانند شرایط کاری مربوطه خود را تحمل کنند، ضروری است. روشهای تست مختلفی وجود دارد که هر کدام برای آزمایش نقص و ضعف طراحی شدهاند. انتخاب روش تست مناسب برای دستیابی به نتایج مطلوب بسیار مهم است. روشهای آزمایش خاص کاربرد در کد یا استاندارد جوش مربوطه که توسط نهادهای حاکم مانند انجمن جوشکاری آمریکا (AWS)، موسسه نفت آمریکا (API) یا انجمن استانداردهای کانادا (CSA) تولید شده است، تشریح شده است.
بازرسی جوشکاری میتواند بر هزینهها و ایمنی در یک پروژه جوشکاری تاثیر بگذارد و به عنوان یک اقدام تضمین کیفیت برای جلوگیری از خطر آسیب شدید یا حتی از دست دادن جان، عمل کند. اشتباهات در فرآیند جوشکاری ممکن است در ابتدا مورد توجه قرار نگیرند، اما پروفیلهای جوش نادرست (به عنوان مثال زیر برش)، تخلخل، ترک، تغییر شکل و سایر عیوب می تواند منجر به از دست دادن استحکام، کاهش دوام و خرابی تجهیزات شود.
روشهای مختلفی برای تست جوش وجود دارد تا اطمینان حاصل شود که محصولات از کیفیت مناسب برای استفاده مورد نظر خود برخوردار هستند. این فرآیند تضمین میکند که پروژهها با استانداردهای ایمنی و عملیاتی خاصی مطابقت دارند، جوشکارها را در طول جوشکاری ایمن نگه میدارد و از کاربران در طول عمر محصول محافظت میکند.
بازرسی چشمی (فرمی از NDT)
بازرسی چشمی اولین و ساده ترین روش برای آزمایش کیفیت جوش است. یک بازرس آموزش دیده سطح جوش را با چشم غیرمسلح یا ابزارهای بزرگنمایی برای هر گونه نقص بصری بررسی میکند، مسائلی که بیش از معیارهای پذیرش بصری است. برخی از شاخصهای رایج نقصهایی که بازرس در بازرسی بصری به دنبال آن میگردد عبارتند از:
- ترکها: در جوشکاری، ترک می تواند در فلز پایه، فلز پرکننده یا هر دو ایجاد شود که از شدیدترین عیوب در جوشکاری هستند و بسیاری از تعمیرات نیاز به برش و تعویض ناحیه ترک خورده دارند.
- آندرکات: فرآیند جوشکاری باعث ایجاد گوج در فلز پایه میشود و جوشکار نمیتواند آنها را پر کند. مقدار قابل قبول آندرکات اغلب بین ۱/۱۶ اینچ و ۱/۳۲ اینچ محدود میشود، اگرچه استانداردها ممکن است متفاوت باشد.
- تخلخل: نشانه شکست احتمالی جوش است و با سوراخهای کوچکی که رو یا زیر سطح جوش پیدا میشود مشخص میگردد.
- ذوب ناقص (Incomplete Fusion): در صورتی که جوش به فلز پایه یا سایر گذرگاه های جوش نفوذ نکند، ذوب ناقص رخ می دهد. هیچ مجوزی برای این نقص وجود ندارد و تقریبا همیشه نیاز به تعمیر فوری دارد.
- نیمرخ نادرست جوش (Incorrect Weld Profile): ناپیوستگیها یا عیوب مانند آندرکات، کم پر شدن، همپوشانی، اندازه جوش نادرست، تقعر بیش از حد یا تقویت بیش از حد همگی نمونههایی از نیمرخ نادرست جوش هستند که با بازرسی چشمی قابل شناسایی است.
بازرسیهای چشمی زمانی که توسط بازرسان آموزش دیده با تجربه در شناسایی شاخصهای بصری انجام میشوند، میتوانند به دقت عیوب را آشکار کنند. علاوه بر این، روشنایی مناسب در حین بازرسی برای جلوگیری از شناسایی نادرست یا مشکلات از دست رفته بسیار مهم است. بازرسی بصری اغلب شامل سه مرحله است:
- بازرسی قبل از جوشکاری: در ابتدای یک پروژه جوشکاری، یک بازرس سعی میکند شرایط نامناسب را قبل از ایجاد مشکلات و تاثیر بر کیفیت جوش شناسایی و اصلاح کند.
- بازرسی جوشکاری: بازرسی در حین عملیات جوشکاری میتواند با ارزیابی و اصلاح شرایط و رویههای جوشکاری از بروز مشکلات جوش تکمیل شده جلوگیری کند.
- بازرسی پس از جوش: هنگامی که یک جوشکاری کامل میشود، بازرسی پس از جوش یکپارچگی آن را تایید نموده که اغلب از روشهای آزمایش غیر مخرب استفاده میگردد و هدف آن شناسایی ناپیوستگیهای ظاهری است.
روشهای تست غیر مخرب (NDT)
آزمایش غیرمخرب فرآیندی برای کنترل کیفیت جوش است که شامل بازرسی یکپارچگی محصول و در عین حال دست نخورده نگه داشتن آن است. به شرطی که یک محصول دارای مشخصات مورد نیاز باشد، پس از اتمام آزمایش همچنان کاربردی خواهد بود، که با به حداقل رساندن نمونه های هدر رفته در زمان و هزینه شرکت صرفه جویی می کند.
بسیاری از روشهای NDT برای کاربردهای مختلف وجود دارد که رایج ترین آنها شامل موارد زیر است:
تست اولتراسونیک (UT)
این تکنیک بازرسی جوشکاری از امواج صوتی با فرکانس بالا برای تشخیص عیوب یا ناهماهنگی در یک جوش استفاده میکند. بازرس یک کوپلنت (couplant) را روی سطح قطعه اعمال و از یک پروب برای آزمایش نقص استفاده میکند. هنگامی که یک موج صوتی با یک نقص مواجه شود، مقداری انرژی به یک مبدل اولتراسونیک منعکس و یک پژواک ایجاد میکند.
ابزار تست زمان انعکاس آن پژواک به کاوشگر را محاسبه کرده و نتایج را بر روی صفحه نمایش مانیتور اولتراسونیک در زمان واقعی ارائه میدهد. سپس بازرس باید ارزیابی کند که آیا این ناپیوستگی دسیبلهایی را بیشتر از آستانهای که کد قابل اعمال تعیین شده ایجاد میکند یا خیر.
این تست مزایای قابل توجهی دارد؛ قابل حمل است و نتایج فوری را ارائه میدهد. همچنین میتواند ترکهای پنهان، حفرهها و همجوشی نامناسب در یک جوش را به طور مداوم شناسایی کند. بازرسان میتوانند سیگنال منعکس شده را به روشهای متعددی اندازه گیری کنند تا اندازه، شکل و ماهیت شکست جوش را تعیین و محل دقیق ناپیوستگیهای داخلی را تعیین کنند.
تست ذرات مغناطیسی (MT)
MT یک روش عالی برای بررسی کیفیت جوش با شناسایی عیوب سطح و نزدیک به سطح در فلز فرومغناطیسی(ferromagnetic) است. بازرس ذرات ریز فرومغناطیسی را روی مواد اعمال نموده و با استفاده از آهنربای دائمی یا آهنربا الکترومغناطیسی در اطراف جوش ایجاد میکند. سپس یک کاوشگر مغناطیسی را روی سطح آن اعمال میکنند. ناپیوستگیهای سطحی، ذرات را به داخل می کشاند و آنها در امتداد نقص ردیف میشوند.
اگر هیچ ذره ای انباشته نشود، هیچ نقص سطحی یا نزدیک به سطح وجود ندارد. خطوط شار مغناطیسی در حضور ناخالصیها تغییر می کنند، فرآیندی که با چشم غیرمسلح نامرئی است. تمیز کردن سطح برای موثر بودن این روش بسیار مهم است و به متخصص نیاز دارد تا الگوهای ذرات آهن را به صورت بصری بررسی کند. تکنسینها گاهی اوقات ذرات فرومغناطیسی رنگی را اضافه میکنند تا عیوب در طول آزمایش آشکارتر شوند. یکی از مزایای اصلی MT این است که نتایج فوری را نشان میدهد و به جوشکاران اجازه می دهد عیوب را در محل اصلاح کنند.
تست نفوذ مایع (PT)
آزمایش مایع نافذ از یک رنگ مایع یا محلول فلورسنت برای تشخیص ناپیوستگیهای سطحی مانند خط مویی و ترکهای میکروسکوپی روی سطح جوش استفاده میکند. بازرس قطعه را تمیز نموده و یک ماده نافذ رنگ را روی جوش اسپری یا قلم مو میکند. پس از خشک شدن اسپری، می توانند با پاک کننده و پارچه اضافی آن را جدا کرده و یک دولوپر(developer) را اعمال کنند. با کنتراست رنگ خشک شده، بازرس میتواند عیوب را در حداقل ۱۰ دقیقه شناسایی کند، زیرا سازنده بر روی ماده نفوذی که در هر شکافی نفوذ کرده است، تاثیر میگذارد.
این فرآیند به مواد شیمیایی و آماده سازی سطح قابل توجهی از جمله حذف رنگ یا هر پوشش اضافی نیاز دارد. انتخاب نافذ و توسعهدهنده مناسب بر اساس مواد و الزامات بازرسی بسیار مهم است، زیرا فرمولهای نافذ مختلف به کاربردهای مختلف بازرسی میپردازند. برخی از نکاتی که باید در نظر بگیرید عبارتند از:
- مواد نافذ: مواد نافذ یا فلورسنت هستند که هنگام قرار گرفتن در معرض اشعه ماوراء بنفش نقص را نشان میدهند، یا قابل مشاهده هستند، حاوی رنگی هستند که کنتراست بالایی با پس زمینه سفید رنگ ایجاد میکند. آنها بر اساس قدرت یا قابلیت تشخیص، و همچنین روش حذف برای مازاد طبقه بندی میشوند. مطمئن شوید که یک گزینه مناسب را بر اساس سطح حساسیت مورد نیاز و روش حذف ترجیحی انتخاب کردهاید.
- توسعه دهندگان: توسعه دهندگان مواد نافذ محبوس شده را از نقص بیرون میکشند و برای تجزیه و تحلیل روی سطح قطعه پخش میکنند. طبقه بندی بر اساس روش کاربرد، مانند پودر خشک حل شده یا معلق در یک مایع است. انتخاب توسعه دهنده مناسب میتواند تاثیر قابل توجهی بر احتمال تشخیص داشته باشد.
تست رادیوگرافی (RT)
رادیوگرافی یا آزمایش اشعه ایکس، روشی موثر برای بررسی کیفیت جوش از نظر عیوب داخلی مانند ترک ها یا آخالها (Inclusion) است. این به بازرسان اجازه میدهد تا هر جنبه ای از جوش را ارزیابی کنند و آن را برای جوش لوله ایده آل میکند. این فرآیند شبیه به اشعه ایکس پزشکی و شامل استفاده از اشعه ایکس یا گاما برای نمایش ساختار داخلی جوش بر روی فیلم عکاسی است. این فیلم تغییرات شکل و رنگ را نشان میدهد که نشان دهنده ناپیوستگیهای مختلف جوش است.
در حالی که RT نمای دقیقی از عیوب ارائه میدهد، شامل تجهیزات تخصصی میشود. کیفیت تصویر بسته به تکنسین متفاوت است. همچنین شامل تشعشعات است و برای جلوگیری از قرار گرفتن در معرض به اقدامات احتیاطی شدید ایمنی نیاز دارد. بسته به قدرت منبع، ناحیه نزدیک در اطراف جوش باید بین ۷ تا ۲۲ متر مسدود شود.
معاینات رادیوگرافی به دانش گستردهای نیاز دارد و تنها رادیوگرافیان آموزش دیده میتوانند نتایج را به طور دقیق تفسیر و به طور ایمن با مواد خطرناک برخورد کنند.
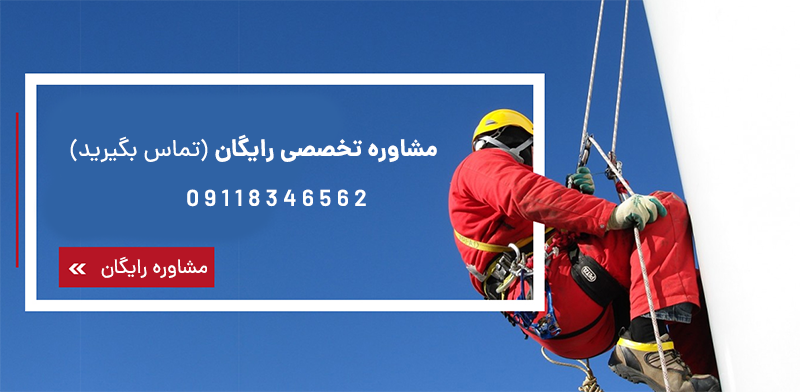
روش های تست مخرب (DT)
آزمایش مخرب مواد را آزمایش میکند و روش های جوشکاری را برای درک عملکرد یک ماده در شرایط خاص بهتر ارزیابی می کند. این فرآیند همچنین توانایی های جوشکار را برای تکمیل یک عملکرد خاص که به عنوان تست جوش نیز شناخته می شود، پوشش می دهد. روشهای DT اغلب در دسترستر از آزمایشهای غیرمخرب هستند و اطلاعات دقیق و تفسیر ساده نتایج را ارائه میدهند.
محصولات تکی برای این نوع آزمایش ایده آل هستند، زیرا آزمایش برای تولید انبوه با این روشها به ندرت از نظر اقتصادی مقرون به صرفه است. برخی از روش های استاندارد DT عبارتند از:
تست کشش
آزمایش مقاومت کششی برای آزمایش استحکام یک اتصال جوش داده شده طراحی شده است که شامل قرار دادن بخشی از جوش آزمایشی در فکهای یک دستگاه تست تخصصی است که نیروی کششی روی نمونه اعمال میکند تا زمانی که بشکند. دستگاههای تست بسته به جوشهایی که برای آزمایش طراحی شدهاند میتوانند قابل حمل یا ثابت باشند.
ماشین به تدریج نیرو اعمال میکند که به یک تصویر گرافیکی از رفتار مواد یا منحنی stress-strain تبدیل می شود. بازرس منحنی stress-strain را برای تعیین کرنش بر روی اجزای آزمایش در لحظاتی که تنش، استحکام کششی نهایی و نقاط شکست را ایجاد میکند، تجزیه و تحلیل میکند.
بسته به نوع و کاربرد جوش، بازرسان می توانند از چندین روش تست کشش، از جمله:
- آزمایش تمام فلزات جوش: این روش فقط فلز جوش یک صفحه آزمایش جوش داده شده نمونه را آزمایش می کند. این یک آزمون استاندارد برای برخی از فرآیندهای صلاحیت روش و فلزات پرکننده است.
- آزمایش کشش عرضی: این فرآیند شامل استخراج میله کششی از محور عرضی صفحه، عمود بر محور جوش، آزمایش برهمکنش بین فلزات پایه و فلزات جوش است.
- آزمایش کشش طولی: همانطور که از نام آن پیداست، این روش نمونه های استخراج شده از محور طولی جوش را آزمایش می کند.
تست خمش
تست خمش استحکام و دوام یک جوش را زمانی که نمونه در معرض نیروهای خمشی قرار میگیرد، ارزیابی میکند. چندین چیز از جمله کیفیت جوش، درجه نفوذ و همجوشی به فلز پایه را با تعیین میزان فشاری که جوش می تواند قبل از شکستن یا شکستگی تحمل کند، اندازه گیری می کند. بسته به کاربرد، بازرسان می توانند از دو نوع آزمایش خمشی اولیه استفاده کنند:
- خم هدایت شده: این روش شامل خم کردن یک نمونه به شعاع خاصی است که معمولا به صورت عرضی به محور جوش گرفته میشود. آزمایشهای خاص متفاوت است، اما نمونه ممکن است در یک دستگاه آزمایشی از نوع پیستونی یا جیگهای پیچیده خم شود. بازرسان بسته به ناحیهای که در کشش قرار می دهند، می توانند سطح یا ریشه جوش را آزمایش کنند که برای یافتن عیوب همجوشی لاینر مفید است و معمولا برای آزمایش روشهای جوشکاری استفاده میشود، زیرا برای اکثر شرایط جوشکاری مورد نیاز است.
- خم آزاد: آزمایش خم آزاد شامل خم کردن یک جوش در جهت مورد نظر و قرار دادن آن به صورت عمودی بین دو صفحه پرس است. فاصله بین صفحات تا زمانی که نمونه موازی شود کاهش می یابد. این به مواد اجازه می دهد تا آزادانه بدون استفاده از قالب یا سنبه خم شوند و در حین بررسی ترک ها و سایر عیوب سطحی، انعطاف پذیری آن را به طور موثر ارزیابی می کنند.
این آزمایشها میتوانند پیشبینی کنند که چگونه یک جوش تحت تنش باقی میماند تا از خرابیهای فاجعهبار جلوگیری کند و ایمنی، کیفیت و ثبات قطعات را ارتقا دهد.
تست ضربه
تست ضربه توانایی جوش را برای جذب انرژی تحت بارگذاری یا ضربه ناگهانی ارزیابی می کند. میتواند استحکام ضربه، مقاومت در برابر شکست و ضربه و چقرمگی جوش را تعیین کند. این روش نسبتا ساده است و اغلب شامل انداختن یک جسم سنگین، مانند چکش، روی نمونه جوش است. ارتفاع افت مقدار انرژی مورد نیاز برای پاره شدن نمونه را تعیین می کند و رفتار شکست را در شرایط مختلف ارزیابی می کند.
در برخی موارد، در صورتی که برای ارزیابی شکنندگی در دماهای پایین ضروری باشد، آزمایش ضربه در دمای آزمایشی خاص انجام می شود. دو نوع اصلی تست ضربه در جوشکاری وجود دارد که عبارتند از:
- تست Charpy V-notch: این تست با نرخ کرنش بالا شامل ضربه زدن به یک نمونه بریده بریده با نوسان آونگ وزن کنترل شده از ارتفاع از پیش تعیین شده است. نمونه به صورت افقی نگه داشته می شود و شکاف آن به سمت پاندول است. استحکام ضربه یک ماده را در صورت وجود نقص و مقدار انرژی مورد نیاز برای شکستن نمونه را تعیین می کند. برای آزمایش مواد انعطاف پذیر مناسب است.
- تست Izod: آزمایش Izod انرژی مورد نیاز برای شکستن فلز را تعیین می کند. بر خلاف تست چارپی، آزمایش Izod نمونه جوش را به صورت عمودی با شکاف رو به آونگ نگه می دارد. این آزمایش برای آزمایش مواد شکننده مفید است.
از کیفیت و یکپارچگی سازهها و اجزای جوش خود اطمینان حاصل کنید
روشهای مختلف بازرسی جوشکاری برای آشکار کردن هرگونه ضعف در محصولات و تجهیزات وجود دارد، و فرآیند آزمایش برای اطمینان از ادامه بهبود کیفیت، ایمنی و قابلیت اطمینان جوشهای حرفهای ضروری است. در حالی که هر روش تست دارای مزایا و معایبی است، انتخاب روش مناسب بر اساس الزامات خاص جوش و استانداردهای صنعتی قابل اجرا برای اطمینان از یک دید کلی دقیق از کیفیت جوش ضروری است.
خواه در ساخت، کنترل کیفیت یا هر زمینه دیگری که به استاندارد بالایی از کیفیت و قابلیت اطمینان نیاز دارد، اولویت بندی آزمایش محصولات شما را ارتقا می دهد و آنها را برای هدف مورد نظرشان ایمن و قابل اعتماد نگه می دارد. اطمینان حاصل کنید که با بازرسان ماهر با تجربه در کار با تجهیزات مورد نیاز برای آزمایش های مختلف جوش کار می کنید.