بازرسی خط لوله فرآیندی حیاتی است که ایمنی، قابلیت اطمینان و اثربخشی خطوط لولهای را که فواصل بسیار زیادی را طی میکنند و مواد مختلفی مانند نفت، گاز، آب و مواد شیمیایی را حمل مینمایند، تضمین میکند. از آنجایی که این خطوط لوله نقش مهمی در زیرساختهای مدرن ما دارند، بازرسی منظم آنها از نظر نقص احتمالی ضروری است. این مقاله به بررسی دنیای بازرسی خطوط لوله میپردازد و روشها، فناوریها و استانداردهای مورد استفاده برای ارزیابی و نگهداری خطوط لوله را مورد بحث قرار میدهد.
بازرسی خط لوله چیست؟
بازرسی خط لوله جزء جدایی ناپذیر مدیریت یکپارچگی خط لوله برای اطمینان از شرایط بهینه آن است. مقررات ایمنی خطوط لوله مانند API 570 این فعالیت های بازرسی را کنترل میکند. در اکثر شرکتها، مرسوم است که خطوط لوله آنها تحت بازرسیهای منظم قرار میگیرند.
هنگام بازرسی خطوط لوله، این فرآیند شامل بررسی و ارزیابی وضعیت، استحکام و عملکرد خطوط لوله مورد استفاده برای اهداف مختلف مانند انتقال سیالاتی مانند نفت، گاز و آب است. این بازرسی شامل خطوط لوله زیرزمینی و زیرزمینی برای تایید عملکرد مناسب و رعایت استانداردهای ایمنی و شناسایی مسائل یا آسیبهای احتمالی میشود.
روند بازرسی خط لوله چگونه کار میکند؟
در طول بازرسی خط لوله، تجهیزات و تکنیکهای تخصصی عواملی مانند یکپارچگی سازه، سطوح خوردگی، نشت و سلامت کلی خط لوله را ارزیابی میکنند. این بازرسیها از اهمیت بالایی برخوردار هستند زیرا به شناسایی هر گونه نقص، ضعف یا حساسیتی که می تواند منجر به شکست خط لوله شود کمک میکند.
روش های مختلف بازرسی خطوط لوله برای ارزیابی ظرفیت عملکرد خطوط لوله طراحی شده است. این رویه ها عبارتند از:
مرحله ۱: بازرسی بصری
بازرسی بصری در بازرسی خط لوله شامل بررسی مستقیم خط لوله با استفاده از حواس بینایی انسان یا دستگاههای نوری است. بازرسان لولهها به صورت بصری سطح خارجی و اجزای داخلی قابل دسترسی را برای عیوب، ناهنجاریها یا علائم آسیب قابل مشاهده ارزیابی میکنند. این مرحله اولیه در بازرسی خط لوله برای تعیین نیاز به آزمایش یا اقدامات تعمیر و نگهداری بیشتر است.
مرحله ۲: آزمایش غیر مخرب (NDT)
آزمایش غیر مخرب (NDT) به عنوان مرحله دوم در بازرسی خط لوله برای تکمیل و افزایش یافتههای بازرسی بصری انجام میشود. در حالی که بازرسی بصری ارزشمند است، ممکن است وضعیت داخلی خط لوله را به طور جامع ارزیابی نکند. روش های متداول NDT شامل:
-
تست اولتراسونیک
آزمایش اولتراسونیک بر روی خطوط لوله انجام میشود تا مسائلی مانند ترک، خوردگی یا تغییر در ضخامت دیوار را ارزیابی کند. این آزمایش از تجهیزاتی استفاده میکند که امواج صوتی با فرکانس بالا را به خط لوله ساطع میکنند و امواجی را که به عنوان نشانهای از مشکلات به عقب بازمیگردند، تجزیه و تحلیل مینماید.
تجهیزات امواج منعکس شده را دریافت کرده و سپس آنها را به سیگنال های الکتریکی تبدیل می کند. سپس این سیگنال ها برای تعیین وجود نقص یا ناهنجاری در خط لوله تجزیه و تحلیل می شوند.
-
تست ذرات مغناطیسی
بازرسی ذرات مغناطیسی روشی برای بازرسی مواد فرومغناطیسی برای تشخیص عیوب سطحی با عبور جریان الکتریکی از آنها است. همچنین می تواند عیوب را که کمی زیر سطح مواد قرار دارند شناسایی کند.
این روش به ویژه در شناسایی عیوب مانند ترکها و ناپیوستگیهای جوش که میتواند یکپارچگی مواد را به خطر بیندازد، موثر است. تست ذرات مغناطیسی را می توان با استفاده از تکنیکهای مختلف، از جمله روشهای تماس مستقیم، تعلیق مرطوب، یا روش های پودر خشک، بسته به ماده مورد بازرسی و نوع نقص مورد نظر انجام داد.
-
تست رادیوگرافی
تست رادیوگرافی (RT) یک تکنیک بازرسی غیر مخرب است که از اشعه ایکس یا اشعه گاما برای تجزیه و تحلیل ترکیب داخلی قطعات ساخته شده و تشخیص هرگونه نقص یا ایراد استفاده میکند.
در تست رادیوگرافی، یک منبع رادیوگرافی، مانند دستگاه اشعه ایکس یا یک ایزوتوپ رادیواکتیو، در یک طرف ماده قرار می گیرد. تابش از ماده عبور می کند و با مناطقی با ضخامت یا چگالی متفاوت تعامل متفاوتی دارد.
در طرف مقابل، یک فیلم رادیوگرافی یا آشکارساز دیجیتال تابش ارسالی را می گیرد. تصویر رادیوگرافی بهدستآمده ساختار داخلی ماده را نشان میدهد و تفاوتهای چگالی مانند حفرهها، ترکها، عیوب جوش یا آخالها را برجسته میکند.
-
آزمایش جریان گردابی
آزمایش جریان گردابی روشی است که از القای الکترومغناطیسی برای تشخیص عیوب در خطوط لوله و لوله ها استفاده میکند. یک کاوشگر به داخل لوله وارد شده و در تمام طول آن حرکت میکند. امپدانس الکتریکی با ایجاد جریانهای گردابی از طریق سیم پیچ های الکترومغناطیسی درون کاوشگر اندازه گیری میشود تا هرگونه تغییر را کنترل کند.
با مطالعه این تغییرات، آزمایش جریان گردابی میتواند عیوب مختلف از جمله ترکهای سطحی، حفرهها، تغییرات ضخامت مواد و تغییرات رسانایی را شناسایی و ارزیابی کند. این تکنیک حساس، کارآمد و قابل استفاده برای مواد رسانای مختلف است که آن را در هوافضا، خودروسازی، تولید و تولید برق ارزشمند میکند.
-
تست هیدرواستاتیک
تست هیدرواستاتیک برای ارزیابی استحکام و تشخیص نشتی در خطوط لوله استفاده می شود. این آزمایش شامل پر کردن تجهیزات با آب، اطمینان از عدم وجود حفره هوا و اعمال یک سطح فشار از پیش تعیین شده برای مدت زمان مشخص است.
در طول آزمایش هیدرواستاتیک، تجهیزات به دقت با آب پر میشوند تا از اشباع کامل اطمینان حاصل شود. فشار آب بالاتر از سطح عملیاتی معمولی است که اغلب بیش از ۱.۵ برابر فشار استاندارد است. این فشار بالا برای مدت زمان معینی، معمولاً چند دقیقه یا چند ساعت، حفظ میشود، در حالی که برای هرگونه افت فشار یا نشانههای نشتی به دقت نظارت میشود.
هدف اصلی آزمایش هیدرواستاتیک تایید این است که تجهیزات می توانند فشار عملیاتی مورد نظر را بدون نشتی یا تغییر شکل قابل توجه تحمل کنند.
-
تست ضربه چارپی
تست ضربه چارپی یک روش استاندارد برای ارزیابی چقرمگی و مقاومت در برابر ضربه مواد، به ویژه فلزات است. این آزمایش به تعیین توانایی مواد برای تحمل بارها یا ضربه های ناگهانی و جذب انرژی بدون شکستگی یا شکستگی کمک میکند.
-
نشت شار مغناطیسی
نشت شار مغناطیسی (MFL) یک روش آزمایش غیر مخرب است که برای بررسی وضعیت مواد فرومغناطیسی مانند خطوط لوله استفاده میشود. این شامل ایجاد یک میدان مغناطیسی قوی در داخل ماده و تشخیص هرگونه نشت شار مغناطیسی ناشی از نقص یا ناهنجاری است.
در طول آزمایش نشت شار مغناطیسی، یک کاوشگر یا سنسور بسیار مغناطیسی در امتداد سطح ماده مورد بازرسی حرکت میکند. همانطور که میدان مغناطیسی با ماده برهمکنش می کند، مسیر کمترین مقاومت را دنبال می کند. اگر هر گونه بی نظمی مانند ترک، خوردگی یا از دست دادن مواد وجود داشته باشد، میدان مغناطیسی نشت می کند یا منحرف می شود و در نتیجه نشت شار قابل توجهی ایجاد میشود.
-
ساعت تست موج هدایت شده
آزمایش موج هدایت شده (GWT) یک روش آزمایش غیر مخرب است که برای بررسی سازههای طولانی مانند خطوط لوله برای عیوب پنهان استفاده می شود. امواج مکانیکی با فرکانس پایین را در امتداد سازه میفرستد که توسط شکل آن هدایت می شود تا مشکلات احتمالی را شناسایی و مکان یابی کند.
در طول آزمایش موج هدایتشده، یک مبدل بر روی سطح بیرونی سازه قرار میگیرد تا امواج مکانیکی تولید کند که در طول آن حرکت میکنند و با هر گونه نقصی در تعامل هستند و بازتاب ایجاد میکنند. سپس این بازتاب ها برای شناسایی مکان، شدت و نوع مسائل مانند خوردگی، نازک شدن یا ترک تجزیه و تحلیل می شوند.
مرحله ۳: بازرسی درون خطی (ILI)
در حالی که روشهای NDT اطلاعات ارزشمندی در مورد وضعیت داخلی خط لوله ارائه میدهند، محدودیتهایی در مورد پوشش و دسترسی دارند. در مقابل، ILI شامل استفاده از دستگاههای پیشرفتهای به نام Smart Pigging است که از طریق خط لوله حرکت میکنند و دادههای مربوط به پارامترهایی مانند ضخامت دیوار، سطوح خوردگی و ویژگیهای داخلی را در تمام طول جمعآوری میکنند. Smart Pigging مجهز به حسگرها و ابزارهایی هستند که عیوب را تشخیص میدهند، ضخامت دیوار را اندازه گیری نموده و خوردگی را تشخیص میدهند.
مرحله ۴: سیستمهای تشخیص نشت
پس از تکمیل ILI، سیستمهای تشخیص نشت برای مکانیابی و شناسایی هر گونه نشتی یا نقض احتمالی در خط لوله بهکار گرفته میشوند. این سیستمها از فناوریهای مختلفی مانند سنسورهای فشار، سنسورهای صوتی یا فلومترها برای نظارت مستمر خط لوله برای هرگونه نشانهای از نشتی استفاده میکنند.
مرحله ۵: تست فشار
آزمایش فشار پس از اجرای یک سیستم تشخیص نشت در بازرسی های خط لوله برای تایید استحکام و یکپارچگی خط لوله در شرایط عملیاتی عادی انجام میشود.
پس از نصب سیستم تشخیص نشت، آزمایش فشار ارزیابی می کند که خط لوله چقدر می تواند فشار عملیاتی مورد نظر را بدون مشکلات مهم تحمل کند.
خط لوله در طول آزمایش فشار تحت فشارهای بالاتری نسبت به فشار عملیاتی معمولی خود قرار میگیرد. این فشار بالا امکان ارزیابی کامل عملکرد خط لوله، شبیه سازی شرایط دنیای واقعی و اطمینان از توانایی آن را برای مدیریت ایمن جریان مورد انتظار سیالات یا گازها فراهم میکند.
مرحله ۶: بازرسی حفاظت کاتدی
بازرسی حفاظت کاتدی پس از آزمایش فشار در بازرسیهای خط لوله برای ارزیابی و حفظ اثربخشی سیستم حفاظت کاتدی در جلوگیری از خوردگی انجام میشود.
پس از اتمام تست فشار، بازرسی حفاظت کاتدی بر محافظت در برابر خوردگی متمرکز است.
حفاظت کاتدی شامل استفاده از جریان مستقیم برای خنثی کردن واکنشهای الکتروشیمیایی است که باعث زوال میشود. انجام بازرسی حفاظت کاتدی پس از آزمایش فشار، تضمین می کند که اقدامات پیشگیری از خوردگی خط لوله به درستی عمل می کند. این بازرسی مستلزم ارزیابی کارایی سیستم، اندازهگیری پتانسیلهای الکتریکی، و بازرسی بصری آندها یا منابع جریان تحت تاثیر است.
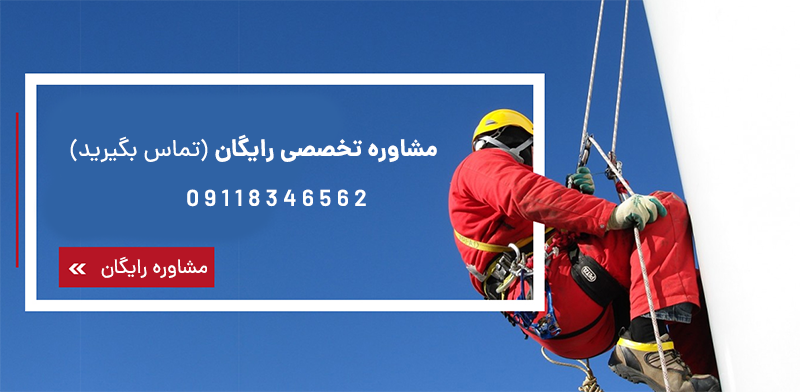
چرا بازرسی خط لوله ضروری است؟
هنگام انجام بازرسی خط لوله، در نظر گرفتن عوامل مختلفی برای اطمینان از ارزیابی جامع وضعیت و عملکرد خط لوله ضروری است. این عوامل عبارتند از:
۱. یکپارچگی ساختاری
ارزیابی یکپارچگی ساختاری خط لوله برای شناسایی هرگونه تغییر شکل، خوردگی یا آسیب مکانیکی که ممکن است بر استحکام و پایداری آن تاثیر بگذارد، ضروری است.
۲. تشخیص نشت
تشخیص نشت یا علائم نشت مایع در طول خط لوله برای جلوگیری از آلودگی محیطی، به حداقل رساندن تلفات و اطمینان از حمل و نقل ایمن بسیار مهم است.
۳. ارزیابی خوردگی
ارزیابی سطح خوردگی در سطوح خط لوله مهم است زیرا خوردگی میتواند مواد را در طول زمان ضعیف کند و خطر شکست یا پارگی را افزایش دهد. ممکن است از تکنیکهایی مانند تست اولتراسونیک یا بازرسی الکترومغناطیسی استفاده شود.
۴. عملکرد عملیاتی
بازرسی باید عملکرد عملیاتی خط لوله، از جمله سرعت جریان، سطوح فشار، و کنترل دما را ارزیابی کند تا از عملکرد صحیح آن اطمینان حاصل شود.
۵. ارزیابی پوشش و عایق
وضعیت پوشش و سیستمهای عایق خط لوله باید ارزیابی شود تا مشخص شود که آیا آنها خط لوله را از عوامل محیطی خارجی مانند رطوبت یا خوردگی محافظت میکنند یا خیر.
۶. ملاحظات ژئوتکنیکی
برای خطوط لوله زیرزمینی، ارزیابی شرایط خاک اطراف، حرکت بالقوه زمین و سایر عوامل خارجی که میتواند بر پایداری و یکپارچگی خط لوله تأثیر بگذارد ضروری است.
۷. رعایت مقررات
فرآیند بازرسی باید بررسی کند که آیا خط لوله با استانداردها، مقررات و کدهای ایمنی مربوطه مطابقت دارد و از رعایت الزامات صنعتی و دولتی اطمینان حاصل کند.
۸. نیاز به تعمیر و نگهداری
شناسایی مناطقی که نیاز به نگهداری یا تعمیر دارند برای رسیدگی سریع به مسائل احتمالی و کاهش خطرات حیاتی است. این شامل شناسایی مناطق با یکپارچگی به خطر افتاده، مفاصل آسیب پذیر یا اجزای آسیب دیده است.
۹. تجزیه و تحلیل داده ها و گزارش
دادههای بازرسی جمعآوریشده باید به دقت تجزیه و تحلیل، تفسیر و مستند شوند تا گزارشی جامع ارائه شود که وضعیت خط لوله را برجسته کند، نگرانیها را شناسایی کند و اقدامات یا استراتژیهای تعمیر و نگهداری مناسب را توصیه کند.
مزایای انجام بازرسی خطوط لوله چیست؟
بازرسی خطوط لوله مزایا و مزایای بی شماری را ارائه می دهد. آنها برای اطمینان از ایمنی، قابلیت اطمینان و کارایی سیستم های خط لوله ضروری هستند. به طور کلی، بازرسی منظم خطوط لوله هفت مزیت دارد:
۱. بهبود ایمنی
بازرسیها خطرات، عیوب یا ضعفهای احتمالی را در خطوط لوله شناسایی میکند، ایمنی کلی را ارتقا ذلذه و خطر تصادف، نشت یا آسیب به مردم و محیط را به حداقل میرساند.
۲. تشخیص زودهنگام مشکل
در مراحل اولیه، بازرسیها عیوب خط لوله مانند خوردگی، ترکها یا خرابیهای مکانیکی را تشخیص میدهند. بازرسان با رسیدگی سریع به این مشکلات، تعمیر و نگهداری پیشگیرانه را امکان پذیر میکنند و احتمال تعمیرات پرهزینه یا خرابی های ناگهانی را کاهش میدهند.
۳. انطباق با مقررات
بازرسیها رعایت مقررات ایمنی و زیست محیطی، نشان دادن انطباق و اجتناب از مجازات های احتمالی یا عواقب قانونی را تضمین میکند.
۴. عملکرد بهینه
بازرسیها ظرفیت جریان، سطوح فشار و یکپارچگی ساختاری را ارزیابی میکنند و از عملکرد موثر خطوط لوله اطمینان میدهند.
۵. صرفه جویی در هزینه
بازرسیهای منظم منجر به صرفه جویی طولانی مدت در هزینهها میشود. با رسیدگی سریع به مسائل جزئی، بازرسیها از تعمیرات مهم و پرهزینهتر جلوگیری میکند. آنها همچنین برنامههای تعمیر و نگهداری را بهینه میکنند، زمان خرابی را کاهش میدهند و طول عمر سیستم خط لوله را افزایش میدهند.
۶. حفاظت از محیط زیست
بازرسیها، نشتها یا منابع بالقوه آلودگی را شناسایی و بررسی میکنند، از محیط زیست محافظت و از نشت یا آلودگی جلوگیری مینمایند.
۷. اعتماد ذینفعان
بازرسیهای معمول نشاندهنده تعهد به ایمنی، قابلیت اطمینان و عملکرد مسئولانه است که باعث ایجاد اعتماد در جوامع، تنظیمکنندهها، سرمایهگذاران و مشتریان میشود.
بازرسی خطوط لوله ایمنی افزایش یافته، تشخیص زودهنگام مشکلات، انطباق با مقررات، عملکرد بهینه، صرفه جویی در هزینه، حفاظت از محیط زیست و اعتماد ذینفعان را ارائه می دهد. آنها اقدامات پیشگیرانهای برای حفظ یکپارچگی خط لوله، تضمین انتقال روان و ایمن سیال یا گاز هستند.
در نتیجه، انجام بازرسیهای مناسب خطوط لوله برای بازرسان لوله کشی بسیار مهم است. این یک وظیفه حیاتی است که یکپارچگی، ایمنی و اثربخشی سیستم های خط لوله را تضمین می کند. از طریق بازرسی های دقیق، می توان عیوب و خطرات احتمالی را شناسایی کرد که امکان تعمیر و نگهداری به موقع را فراهم میکند.